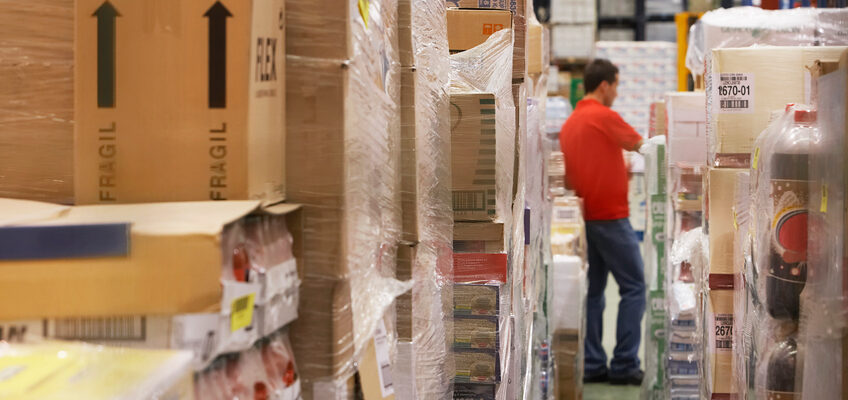
Vendor Managed Inventory (VMI) systems offer benefits that are not achievable in a traditional supply chain configuration. With the transparency gained from Electronic Data Interchange (EDI), manufacturers and distributors can project customer demand to produce and ship the required inventory to prevent out-of-stock situations. The result is the right products reach the right location at the right time.
For example, a manufacturer anticipates the inventory requirements of the distributor as real time sales data is received. Monitoring this, the manufacturer can schedule raw material, production and outbound freight to ensure the correct quantity of product reaches the distributor in time for shipment to the end user.
Reduced Inventory Costs
What are the financial benefits of VMI for Distributors?
In a VMI network, each link of the supply chain can anticipate when stock replenishment is required. When this level of uncertainty is reduced, manufacturers and distributors can operate with reduced inventories of raw material and finished products. Without real time information, the same distributors tend to “load up” with safety stock to avoid being out of stock when a larger-than-anticipated order comes through.
As transparency improves, the total average inventory cost in the system can be reduced.
Automatic Ordering: Reduced Human Error
With Vendor Managed Inventory, traditional “ordering” is eliminated. As distributor stocks reach predetermined levels, the supplier automatically produces and ships to replenish the distributor’s inventory as needed. Employee workloads are reduced and keystroke errors are eliminated.
(Learn more about NeoGrid’s VMI Solutions and how we can help you optimize your order and logistics processes.)
Increased Distributor Velocity: Improving Space Efficiency
For distributors, the benefits of VMI are realized from nearly “just-in-time” operations. With a clear picture of the depletion rate of inventory at the retail customer location, distribution centers can turn inventory at a faster rate while anticipating upcoming deliveries. With continuous throughput, the storage space required is reduced since in-house safety stock can be reduced to minimal levels.
Optimizing Deliveries
To optimize delivery costs, the customer and distributor first evaluate and agree upon maximum inventory levels at the retail location. Weighing this against the normal depletion or sales rate and cost-per-mile, the frequency of deliveries may depend upon the actual distance or driving time from the retail locations. If the rate of sales change due to a promotion, delivery frequency or order sizes may increase.
The transparency derived from VMI has proven to benefit all links in the supply chain by reducing costs and improving service levels.
Want to learn the latest news and industry insights from NeoGrid? Subscribe to the NeoGride Supply Chain Blog and receive weekly informative updates about everyday issues of business, industry trends, success stories and more.