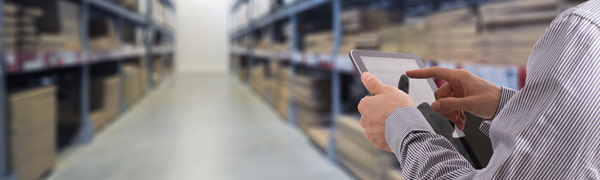
In today’s economic environment, you cannot continue doing what you’ve always done and expect to remain competitive. That’s because supply chain management is evolving. Considering the pressure to contain costs without compromising results, rather than simply improve, any organization that wishes to remain best in class must transform it’s operations. You need to adopt new philosophies, processes, and methods – collectively known as supply chain best practices.
These best practices include:
1. Outsource non-core functions and processes
Outsourcing and off-shoring have come under heavy criticism lately. But if strategically aligned and properly managed, outsourcing non-core functions has the potential to dramatically lower production costs and increase flexibility while allowing you to focus on core competencies.
2. Establish key performance indicators
You can’t expect to improve if you don’t know how you’ve been performing. For this reason, it is critical that supply chain management establishes a robust set of metrics and key performance indicators (KPIs) to drive the right behavior and ensure accountability.
3. Make technology work for you
Many organizations purchase the latest supply chain technologies and then structure their workflows and processes around these chosen technologies. That’s a wrong approach. The right approach is to review your processes and then purchase technologies that satisfy those process needs.
(Still want to know more? Learn about six more Supply Chain Management Best Practices.)
4. Engage in collaborative strategic sourcing
Strategic sourcing which involves consolidating suppliers is considered the fastest way to save money, increase profit margins, and improve operating profits. Collaborative strategic sourcing which requires active involvement of your “internal” customers in the decision making process can further increase operating profits by increasing responsiveness to changing customer needs.
5. Plan for reverse logistics
Inevitably, there will be a flow of products back to suppliers and vendors when items are unsatisfactory or defective, or for reuse or recycling. You need to plan for such processes. Organizations that don’t plan for reverse logistics risk lowering customer experiences, face increased labor activities, and ultimately, may incur revenue losses.
6. Take “green” initiatives and social responsibility seriously
Initially, reducing supply chain carbon footprint was just a “nice” practice. That’s no longer the case. Today, consumers are taking environmental impact into consideration when choosing suppliers. The same applies to social responsibility. A company that ignores its social responsibility risks backlash from workers as well as consumers.
Summary
Some of these best practices might be familiar; others may be new to your organization. Implement all of them and you’ll have a solid foundation for supply chain excellence.
Download our cloud integration white paper to learn the five reasons S&OP belongs in the cloud.