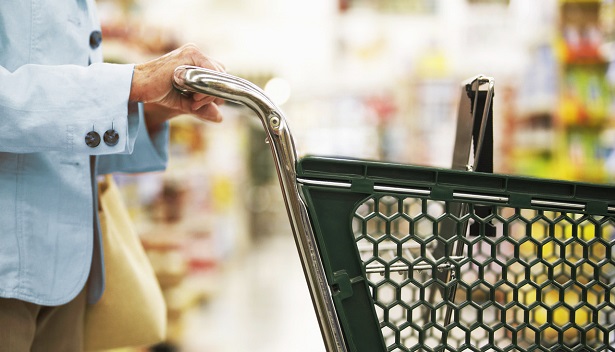
The out-of-stock indicator shows the percentage of product shortage related to total items in a store.
This product shortage in the supply chain impacts consumers, who stop buying the product because it is not on the shelf. The manufacturing sector loses, retail loses and the end consumer loses. To avoid this scenario, the recommendation is that manufacturers and retailers join forces in a collaborative effort to minimize out-of-stocks in retail. But how do you ensure that products are available on the shelf?
There are good practices and technologies to manage out-of-stock indicators. With the support of a good technology solution for supply chain management, you can take actions to prevent product shortages:
- Monitoring the inventory level of manufacturing products in retail. Through restock reports, you can immediately know which products have the highest consumption, which store sells more of a particular item and the inventory coverage numbers. As a result, you identify in advance a possible product shortage on the point of sale shelves and can offer the retailer a replacement product in a timely manner, preventing out-of-stocks and negative impacts for the consumer.
- Identify products with phantom inventory levels (indicator that shows the difference between the number of products in the store’s information system and the amount that, physically, is available for sale to consumers). In the restock report it’s possible to highlight phantom inventory items and take actions focused on these products – as delivering the report to the manufacturing sales promoter working in retail to check if there is stock available for these products in the back of the store.
- The third action is to encourage within retail the physical inventory count of phantom inventory items, and adjust the amount in the inventory management system. The sales associate can act proactively, counting the items on the shelf, and thus making the adjustment collaboratively.
To further add to the management of out-of-stock indicators, it is important to have reports that show the trend of out-of-stock indicators by region and by store. With this data in hand it is possible to monitor whether the actions taken are having an effect, therefore directing, collaboratively with retailers, actions for the stores with larger out-of-stock numbers. To support the decision making of those responsible for supplying the store, the ideal scenario is to use a daily report with the main out-of-stock cases by product and by store.
The technology applied to effective supply chain management solutions, combined with collaborative behavior, helps to tremendously improve the out-of-stock indicators in the chain. With preventive measures and in a timely manner, it’s possible to keep the product on the shelves with little effort, generating gains for manufacturers, retailers and the end consumer.
Download our retail supply chain collaboration white paper to learn the seven most important criteria in selecting a new supply chain platform.