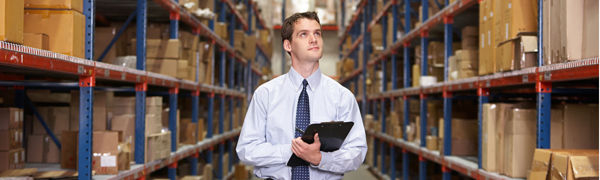
Over the past couple of years, vendor managed inventory (VMI) programs have been gaining in popularity. Because the connections they support have the proven ability to reduce inventory amounts at both the production and distribution level, while ensuring on-shelf availability for retailers, their initial acceptance was enthusiastic. However, the equipment required to orchestrate a cooperative relationship between supply chain partners was cost-prohibitive for many companies, which stifled overall adoption. It is the advent of cloud-based, inventory management software that has renewed interest in this effective collaborative tool.
Understanding how inventory management software works within a VMI platform can help you ascertain the advantages of the system and recognize how it can transform your performance metrics and lower your inventory costs.
Intelligent Connections that Build Profitable Relationships
VMI software works as a cooperative tool between suppliers and retailers. But unlike previous versions that were reactive in nature, new cloud-based platforms enable real-time transmissions, so that you receive point-of-sale and other inventory data immediately. This type of visibility at the store level establishes actionable information that allows you to adjust your production and shipping operations according to the volatile need. Inventory management software helps companies realize:
- Improved fill rates
- Lowered administrative expenses
- Increased on-shelf availability
- Eliminated overstock, out-of-stocks, and phantom inventories
Increased Productivity and Service
Because inventory management software is equipped with intelligent reporting capabilities, you’re armed with heightened decision making and planning information. Daily sales and inventory reports can be transmitted between suppliers and retailers so that everyone is on the same page regarding inventory locations and amounts. This establishes the means to streamline your supply chain activity and replenishment processes for improved customer service.
Since a large portion of assets are usually represented by inventory, intelligent forecasting helps lower stock levels for increased cash flow. Automated order generation (similar to a Kan-Ban system) ensures that on-shelf availability is maintained, and users see up-to-date information via friendly dashboards. The entire system streamlines operations while reducing the time and expense required for supply chain management.
Inventory management software also offers heightened data security through cloud-based storage and execution. Manufacturers, distributors, and retailers that implement a software defined system see impressive returns that provide long-term savings. Orchestrating your supply chain through a cooperative management platform essentially gives you the power to streamline your activities and reduce your operating costs.
Download our retail supply chain collaboration white paper to learn the seven most important criteria in selecting a new supply chain platform.