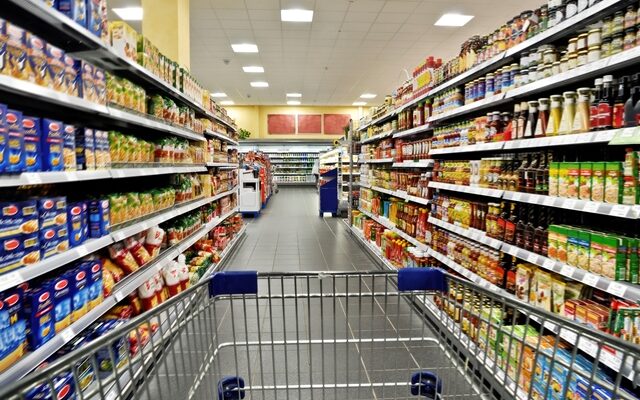
Out-of-stocks (OOS) have negatively impacted the retail industry for decades despite advances in information technology and data availability. Often, the issue of OOS is dealt with as a short-term issue rather than a systematic issue that can be prevented through understanding and correcting its root cause. By shifting the focus of on-shelf-availability (OSA) from triage to prevention, manufacturers and retailers can increase OSA rates, shopper satisfaction and overall profitability.
In order to proactively manage OOS, it is important to identify and understand the root cause of the situation. OOS can be caused by any number of issues including phantom inventory, supply chain disruptions and underestimating demand for a product. The primary goal of a root cause analysis is to determine why and where the problems are occurring. The impact of OOS on sales performance can be crucial to survival in the retail market.
Using a proactive OSA model helps manufacturers and retailers identify and solve the main root causes they face including:
- Phantom Inventory
- Inventory not being available on store shelves
- OOS in store due to OOS at the distribution center
- OOS in store due to order not placed from store to the distribution center
- OOS in store due to order placed on time but not delivered within lead time by supplier
- OOS in store due to order not placed from store to distribution center
- OOS in store due to order on time but not delivered by distribution center
- OOS in store due to OOS in distribution center
To learn more about how the OSA model can help manufacturers and retailers, download Neogrid, North America’s latest White Paper, “OSA: Avoid Lost Sales Due to Out-of-Stocks.”