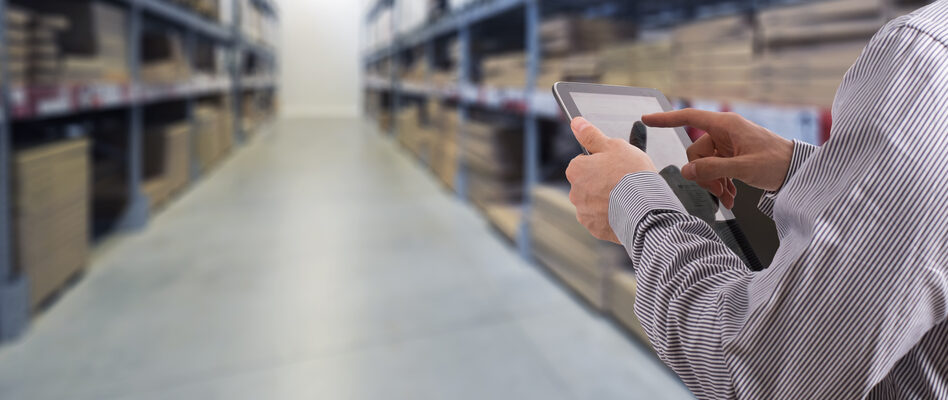
The traditional supply chain consisted of individual value-adding links operating independently with “seat-of-the-pants” forecasting, multiple suppliers, estimated lead times and efficient production runs. A retailer initiated the cycle by predicting the number of orange widgets that will be sold in the coming period and placing an order for delivery at a specific time. The manufacturer either shipped the product from his existing inventory or scheduled a production run. That assumes, of course, that there was enough raw material on hand to produce.
The raw material suppliers would then receive orders for more product to ship to the manufacturer.
But, if the supplier was out of stock for any single component, the whole process ground to a halt. Massive inventories at every level were the answer to 100% order fulfillment.
What is Vendor Managed Inventory?
Information, communication and holistic thinking have changed this process. Using real time inventory data and forecasting, each element of the supply chain is able to minimize the amount of inventory on-hand, organize efficient productions and schedule deliveries in a just-in-time manner.
Letting each component of the supply chain peer forward into real-time sales and inventory levels of the links ahead allows each to proactively plan, produce and ship the forecasted quantities that will be required at the next level.
Inventory optimization contributes to lower costs through the elimination of emergency production scheduling and shipping, better raw material purchasing and reducing the entire supply chain inventory costs.
Challenges to Creating a Vendor Managed Inventory System?
There are challenges to creating a true VMI System. The first is overcoming the paradigm of sharing what may be considered proprietary information. A true, confidential partnering relationship must evolve at each level to ensure mutual trust, continuity of supply and cost reduction at each level.
(Learn more about NeoGrid’s VMI Solutions and how we can help you optimize your order and logistics processes.)
Secondly, there is a cost to linking suppliers in a meaningful way with the necessary systems to access current inventories and forecasting. In some cases, supplier representatives may actually manage the retailer’s inventory in person.
Safety Stock
Things happen. A surge in sales, an unexpected breakdown and long lead-time for a component requires some inventory optimization at every level. Safety stock is the amount of product that must be in place to ensure that a stock-out never occurs. These levels are calculated as a function of demand variability, lead-time and lead-time variability.
Want to learn the latest news and industry insights from NeoGrid? Subscribe to the NeoGride Supply Chain Blog and receive weekly informative updates about everyday issues of business, industry trends, success stories and more.